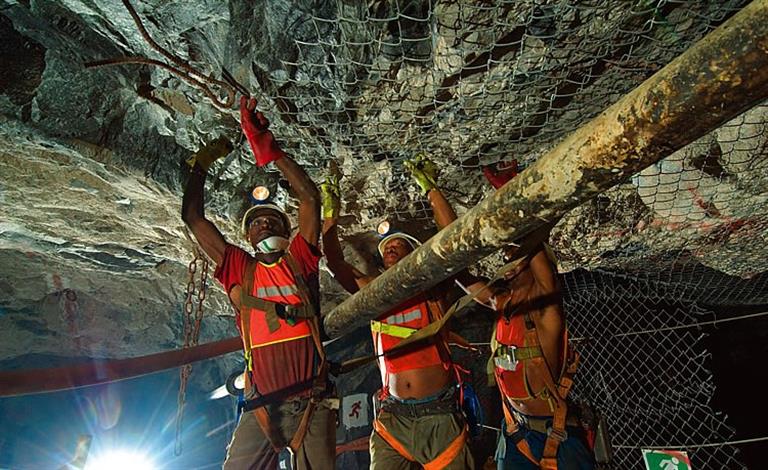
Supply chain underdevelopment in Africa remains a major challenge for societal development and a large barrier to entry for international firms. Yet, with promising resource and growth pockets across the continent in the last decade and the continental population setting to double by 2050, it would be remiss of procurement leaders from any industry to overlook such an exciting continent in 2016 and beyond, from either a supply or customer perspective.
Regional Differences
When assessing the African climate for one’s industry, it would be fatal to use a broad-brush approach. Whilst Africa’s growth as a whole has been indeed held back by the hesitant global economy and political and social conflicts (including the recent Ebola outbreak), there are wide differences in infrastructure, resource pools and democratic stability across the continent. The African Economic Outlook (AEO) predicts a combined GDP growth of 5% in 2016 (a return to pre-2008 levels), crediting increased political stability, refined economic policies and a high demand for commodities. However, Africa’s economy is not homogenous, and given few individual markets provide scale across Africa, it is vital to assess based on the granularity of regions and individual countries in order to identify the true, unique opportunities that Africa presents.
Opportunities
Improved economic policies and stable governance continues to prove exceptionally effective in promoting economic growth in Africa. Resource-poor countries, such as Ethiopia and Rwanda, have managed to sustain GDP growth levels of 8% or more in recent years through effective structural adjustment and economic policies that are reassuring foreign investors, allowing them to tap into Africa’s low labor costs without assuming unacceptable business risk. As many African countries enjoy unprecedented growth levels, the amount of domestic consumption is skyrocketing, both in private goods and public infrastructure, which strengthens the export as well as import potential for foreign investors.
Diversification is another key factor facilitating sustainable growth for Africa’s ‘shining stars’. Nigeria, a leading country accelerating African economic growth in the present day, has managed to maintain strong (6%+) growth in recent years despite continual falls in oil prices (which once made up the majority of Nigeria’s export market). The share of services contributing to Nigeria’s GDP has doubled since 2008. Both resource-rich and resource-poor countries are recognizing that market diversification is essential in macroeconomic stability and to address society’s own consumptive needs. Exploitation of faster and cheaper information and communicative technologies is allowing African countries to become competitive players in the service industry.
Challenges
Despite significant diversification, agriculture remains Africa’s largest sector and still accounts for 25% of GDP as well as 60% of the workforce. The sector is inherently risky, especially for a continent that comparatively lacks many modern technologies used in the rest of the world to secure yield and crop health during adverse conditions. In addition, the price inelasticity of agricultural and mineral commodities leaves these sectors at constant risk of price drops, reducing revenues to Africa’s commodity exporters (as witnessed throughout 2014).
Manufacturing is a sector that is still struggling to take off as a whole across Africa. This is due to a lack of solid infrastructure required for effective production and logistics. Road network quality, reliable power supply and workforce skill still lag behind the rest of the world across the majority of the continent. The Ebola outbreak meant many steps backwards, as production was slowed if not completely cut in most affected areas, resulting in increasing instability and reversing improvements in the business environment.
In summary, Africa holds much potential in 2016 and beyond as a supply chain and investment partner. However, it is vital to assess entry using both country- and industry-specific lenses in order to exploit the unique potential of the continent whilst in full control of the risks.